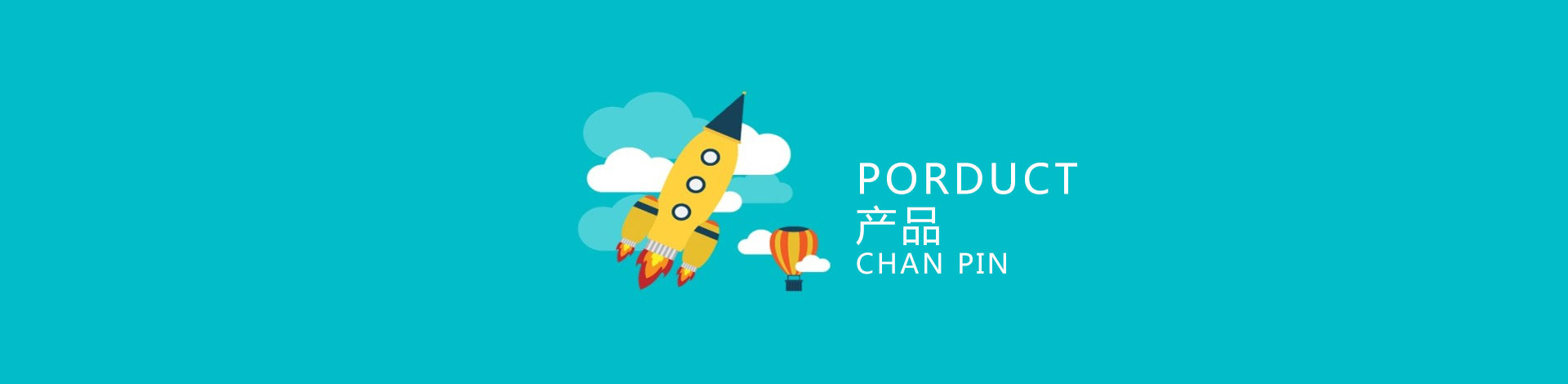
Search
Products
NEWS
hot key words
- Source:
- Date: 2022-07-10
In the process of PCBA processing, the selection of tin penetration is very important. In the through-hole plug-in process, the tin penetration of the PCB board is not good, which is easy to cause problems such as virtual soldering, tin cracking and even parts drop. So what aspects need to be grasped in tin penetration?
1. PCBA tin penetration requirements
According to the IPC standard, the tin penetration requirement of pcba through-hole solder joints is generally above 75%, that is to say, the tin penetration standard for the appearance inspection of the panel surface is not less than 75% of the aperture height (plate thickness), and the pcba Through tin is suitable at 75%-100%. While the plated through hole is connected to the heat dissipation layer or the heat dissipation layer for heat dissipation, the pcba penetration tin requires more than 50%.
Second, the factors that affect the tin penetration of pcba
The tin penetration of pcba is mainly affected by factors such as material, wave soldering process, flux, manual soldering and so on.
A specific analysis of the factors that affect the tin penetration of PCBA:
1. Materials
The tin melted at high temperature has strong permeability, but not all welded metals (PCB boards, components) can penetrate in, such as aluminum metal, its surface generally automatically forms a dense protective layer, and the internal molecules The difference in structure also makes it difficult for other molecules to penetrate. Second, if there is an oxide layer on the surface of the metal to be welded, it will also prevent the penetration of molecules. We generally treat it with flux or brush it with gauze.
What are the factors of PCBA processing through tin?
2. Flux
Flux is also an important factor affecting poor tin penetration of PCBA. Flux mainly plays the role of removing surface oxides of PCB and components and preventing re-oxidation during soldering. The selection of flux is not good, the coating is uneven, and the amount is too small. All will lead to poor tin penetration. You can choose a well-known brand of flux, the activation and wetting effect will be higher, which can effectively remove the oxides that are difficult to remove; check the flux nozzle, the damaged nozzle needs to be replaced in time, and ensure that the surface of the PCB is coated with an appropriate amount of flux. Give full play to the fluxing effect of flux.
3. Wave soldering
The poor tin penetration of pcba is naturally directly related to the wave soldering process. Re-optimize the welding parameters with poor tin penetration, such as wave height, temperature, welding time or moving speed. First, the track angle should be lowered appropriately, and the height of the wave crest should be increased to increase the amount of contact between the liquid tin and the solder end; then, the temperature of the wave crest should be increased. Generally speaking, the higher the temperature, the stronger the penetration of tin, but this should be considered The withstand temperature of the components; finally, the speed of the conveyor belt can be reduced, the preheating and soldering time can be increased, so that the flux can fully remove oxides, wet the solder ends, and increase the amount of tin.
What are the factors of PCBA processing through tin?
4. Manual welding
In the actual plug-in welding quality inspection, a considerable part of the weldment only forms a cone on the surface of the solder, but no tin penetrates into the via hole. In the functional test, it is confirmed that many of these parts are false welding, which is mostly caused by manual plug-ins. In welding, the reason is that the temperature of the soldering iron is not appropriate and the welding time is too short. Poor tin penetration of PCBA can easily lead to virtual soldering problems and increase the cost of rework. If the requirements for pcba tin penetration are relatively high and the welding quality requirements are relatively strict, selective wave soldering can be used, which can effectively reduce the problem of poor pcba penetration.
1. PCBA tin penetration requirements
According to the IPC standard, the tin penetration requirement of pcba through-hole solder joints is generally above 75%, that is to say, the tin penetration standard for the appearance inspection of the panel surface is not less than 75% of the aperture height (plate thickness), and the pcba Through tin is suitable at 75%-100%. While the plated through hole is connected to the heat dissipation layer or the heat dissipation layer for heat dissipation, the pcba penetration tin requires more than 50%.
Second, the factors that affect the tin penetration of pcba
The tin penetration of pcba is mainly affected by factors such as material, wave soldering process, flux, manual soldering and so on.
A specific analysis of the factors that affect the tin penetration of PCBA:
1. Materials
The tin melted at high temperature has strong permeability, but not all welded metals (PCB boards, components) can penetrate in, such as aluminum metal, its surface generally automatically forms a dense protective layer, and the internal molecules The difference in structure also makes it difficult for other molecules to penetrate. Second, if there is an oxide layer on the surface of the metal to be welded, it will also prevent the penetration of molecules. We generally treat it with flux or brush it with gauze.
What are the factors of PCBA processing through tin?
2. Flux
Flux is also an important factor affecting poor tin penetration of PCBA. Flux mainly plays the role of removing surface oxides of PCB and components and preventing re-oxidation during soldering. The selection of flux is not good, the coating is uneven, and the amount is too small. All will lead to poor tin penetration. You can choose a well-known brand of flux, the activation and wetting effect will be higher, which can effectively remove the oxides that are difficult to remove; check the flux nozzle, the damaged nozzle needs to be replaced in time, and ensure that the surface of the PCB is coated with an appropriate amount of flux. Give full play to the fluxing effect of flux.
3. Wave soldering
The poor tin penetration of pcba is naturally directly related to the wave soldering process. Re-optimize the welding parameters with poor tin penetration, such as wave height, temperature, welding time or moving speed. First, the track angle should be lowered appropriately, and the height of the wave crest should be increased to increase the amount of contact between the liquid tin and the solder end; then, the temperature of the wave crest should be increased. Generally speaking, the higher the temperature, the stronger the penetration of tin, but this should be considered The withstand temperature of the components; finally, the speed of the conveyor belt can be reduced, the preheating and soldering time can be increased, so that the flux can fully remove oxides, wet the solder ends, and increase the amount of tin.
What are the factors of PCBA processing through tin?
4. Manual welding
In the actual plug-in welding quality inspection, a considerable part of the weldment only forms a cone on the surface of the solder, but no tin penetrates into the via hole. In the functional test, it is confirmed that many of these parts are false welding, which is mostly caused by manual plug-ins. In welding, the reason is that the temperature of the soldering iron is not appropriate and the welding time is too short. Poor tin penetration of PCBA can easily lead to virtual soldering problems and increase the cost of rework. If the requirements for pcba tin penetration are relatively high and the welding quality requirements are relatively strict, selective wave soldering can be used, which can effectively reduce the problem of poor pcba penetration.
company culture
Jetek Group is a professional manufacturer of PCBs (Included 1-14 layer boards, HDI boards, rigid-flex boards, aluminum boards and so on). Our company was established in 1993 and located in Gaoyao, Zhaoqing. We have a series of fully automatic production equipments and rich PCBs production experience. Flexible order size, fast delivery time, stable quality and competitive price helped us to keep long-term coopertation with our customers.
Technical Information>>
contact us
Jetek Group
Factory 1: No.2, Ma'an Development Zone, 324 National Highway, Gaoyao, Guangdong, China
Factory 2: Building 16, No.16 of Chuangxin Road, Changzhou Street, Rongchang, Chongqing, China
Tel: 008618926528037
Email: mkt01@jetekgroup.com
Overseas Sales Department
Email: info@jetekgroup.com
Tel: +86 0755-23724940
Factory 1: No.2, Ma'an Development Zone, 324 National Highway, Gaoyao, Guangdong, China
Factory 2: Building 16, No.16 of Chuangxin Road, Changzhou Street, Rongchang, Chongqing, China
Tel: 008618926528037
Email: mkt01@jetekgroup.com
Overseas Sales Department
Email: info@jetekgroup.com
Tel: +86 0755-23724940
Products
>>
Copyright © Jetek Group
Address: Building 16, No.16 of Chuangxin Road, Changzhou Street, Rongchang, Chongqing, China
Address: Building 16, No.16 of Chuangxin Road, Changzhou Street, Rongchang, Chongqing, China
本站部分图文来源网络,如有侵权问题请通知我们处理!
网站建设维护