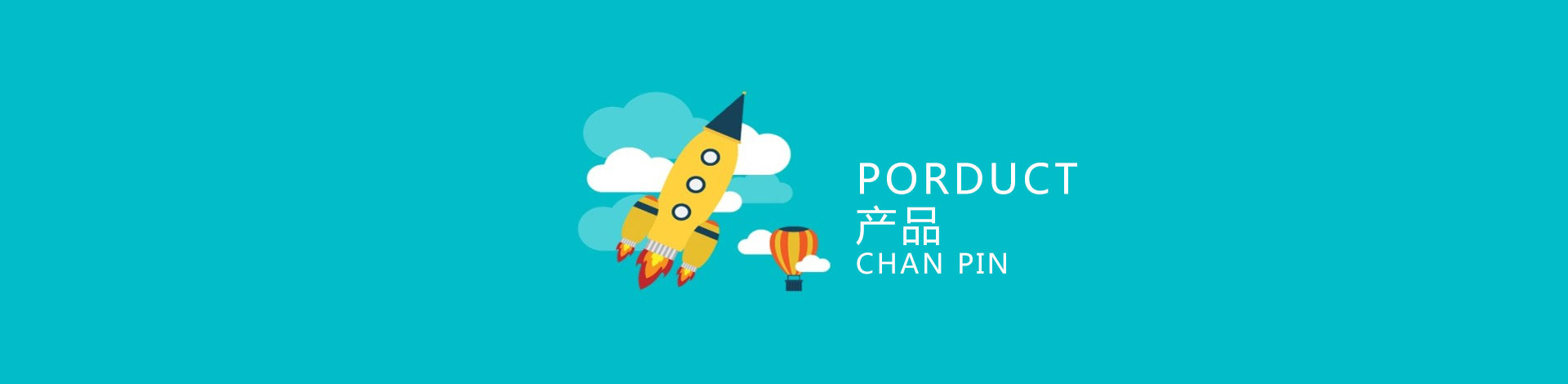
Search
Products
- Source:
- Date: 2022-07-10
In the production process of PCBA circuit boards, it is necessary to rely on a lot of machinery and equipment to assemble a board. Often, the quality level of a factory's machinery and equipment directly determines the manufacturing capacity.
The basic equipment required for PCBA production includes solder paste printer, placement machine, reflow soldering, AOI detector, component angle cutter, wave soldering, tin furnace, board washer, ICT test fixture, FCT test fixture, Aging test racks, etc., PCBA circuit board processing plants of different scales will be equipped with different equipment.
Electronic factory PCBA production equipment
1. Solder Paste Printer
Modern solder paste printing machines are generally composed of plates, solder paste, embossing, circuit board transmission and other mechanisms. Its working principle is: first fix the circuit board to be printed on the printing positioning table, then the left and right scrapers of the printing machine will leak the solder paste or red glue to the corresponding pad through the stencil. The transfer table is input to the placement machine for automatic placement.
The cleaning processes included in the solder paste printing machine include: wiping the bottom of the solder paste printing machine (water-based cleaning agent W2000), and offline cleaning of the solder paste stencil (W1000/EC-200).
What electronic accessories are needed in the production process of PCBA circuit boards?
2. Mounter
Mounter: also known as "mounter", "surface mount system" (Surface Mount System), in the production line, it is configured after the solder paste printer, it is to move the placement head to accurately mount the surface mount components. A device placed on a PCB pad. Divided into manual and automatic two.
3. Reflow soldering
There is a heating circuit inside the reflow soldering, which heats the air or nitrogen to a high enough temperature and blows it to the circuit board with the components attached, so that the solder on both sides of the components is melted and then bonded to the motherboard. The advantages of this process are that the temperature is easy to control, oxidation can be avoided during the soldering process, and the manufacturing cost is easier to control.
Reflow furnace workshop site of SMT production line
4. AOI automatic optical detector
The full name of AOI (Automatic Optic Inspection) is automatic optical inspection, which is a device that detects common defects encountered in welding production based on optical principles. AOI is a new type of testing technology, but it is developing rapidly. Many manufacturers have launched AOI automatic optical inspection equipment.
During automatic detection, the machine automatically scans the PCB through the camera, collects images, and compares the tested solder joints with the qualified parameters in the database. After image processing, the defects on the PCB are checked, and the defects are displayed/marked through the display or automatic sign. Come out for repairs by maintenance personnel.
5. Component cutting machine
6. Wave soldering
7. Tin furnace
In general, tin furnace refers to a welding tool used in electronic welding. For discrete component circuit boards, the welding consistency is good, the operation is convenient, fast, and the work efficiency is high. It is a good helper for your production and processing.
8. Plate washer (ultrasonic or pass-through spray cleaning machine)
It is used to clean the PCBA circuit board, which can remove the pollutants and residues on the board after welding. Improve and guarantee the reliability of PCBA circuit boards.
W3000 is a new type of environmentally friendly water-based product developed by Shenzhen Heming Technology Co., Ltd. independent research and development patent technology. It breaks the cleaning method that requires heating for conventional PCBA water-based cleaning agents. Ideal cleaning effect with short cleaning time and high efficiency.
It has a very good ability to remove various types of no-clean solder paste residues, flux residues, oil stains, fingerprints, metal oxide layers, and particles such as electrostatic particles and dust. With the ultrasonic cleaning process, it can be used for high-cleaning cleaning of camera modules and other high-precision, high-density, assembled with microBGAs, Flip-Chips and other high-tech components
9. ICT test fixture
ICT Test is mainly to detect the open circuit, short circuit and soldering of all parts of the PCBA by contacting the test probe with the test point of the PCB layout.
10.FCT test fixture
FCT (Functional Test) It refers to providing a simulated operating environment (excitation and load) to the test target board (UUT: Unit Under Test), making it work in various design states, so as to obtain the parameters of each state to verify the UUT A method of testing the functionality of a good or bad. Simply put, it is to load the UUT with suitable excitation and measure whether the response of the output terminal meets the requirements.
11. Aging test stand
The aging test stand can test PCBA boards in batches, and simulate the operation of users for a long time to test out the PCBA boards with problems.
12. The cleaning process includes
Wipe the bottom of the solder paste printing machine, clean the solder paste stencil, clean the red glue stencil, clean the fixture carrier, clean the PCB circuit board, etc.
The basic equipment required for PCBA production includes solder paste printer, placement machine, reflow soldering, AOI detector, component angle cutter, wave soldering, tin furnace, board washer, ICT test fixture, FCT test fixture, Aging test racks, etc., PCBA circuit board processing plants of different scales will be equipped with different equipment.
Electronic factory PCBA production equipment
1. Solder Paste Printer
Modern solder paste printing machines are generally composed of plates, solder paste, embossing, circuit board transmission and other mechanisms. Its working principle is: first fix the circuit board to be printed on the printing positioning table, then the left and right scrapers of the printing machine will leak the solder paste or red glue to the corresponding pad through the stencil. The transfer table is input to the placement machine for automatic placement.
The cleaning processes included in the solder paste printing machine include: wiping the bottom of the solder paste printing machine (water-based cleaning agent W2000), and offline cleaning of the solder paste stencil (W1000/EC-200).
What electronic accessories are needed in the production process of PCBA circuit boards?
2. Mounter
Mounter: also known as "mounter", "surface mount system" (Surface Mount System), in the production line, it is configured after the solder paste printer, it is to move the placement head to accurately mount the surface mount components. A device placed on a PCB pad. Divided into manual and automatic two.
3. Reflow soldering
There is a heating circuit inside the reflow soldering, which heats the air or nitrogen to a high enough temperature and blows it to the circuit board with the components attached, so that the solder on both sides of the components is melted and then bonded to the motherboard. The advantages of this process are that the temperature is easy to control, oxidation can be avoided during the soldering process, and the manufacturing cost is easier to control.
Reflow furnace workshop site of SMT production line
4. AOI automatic optical detector
The full name of AOI (Automatic Optic Inspection) is automatic optical inspection, which is a device that detects common defects encountered in welding production based on optical principles. AOI is a new type of testing technology, but it is developing rapidly. Many manufacturers have launched AOI automatic optical inspection equipment.
During automatic detection, the machine automatically scans the PCB through the camera, collects images, and compares the tested solder joints with the qualified parameters in the database. After image processing, the defects on the PCB are checked, and the defects are displayed/marked through the display or automatic sign. Come out for repairs by maintenance personnel.
5. Component cutting machine
6. Wave soldering
7. Tin furnace
In general, tin furnace refers to a welding tool used in electronic welding. For discrete component circuit boards, the welding consistency is good, the operation is convenient, fast, and the work efficiency is high. It is a good helper for your production and processing.
8. Plate washer (ultrasonic or pass-through spray cleaning machine)
It is used to clean the PCBA circuit board, which can remove the pollutants and residues on the board after welding. Improve and guarantee the reliability of PCBA circuit boards.
W3000 is a new type of environmentally friendly water-based product developed by Shenzhen Heming Technology Co., Ltd. independent research and development patent technology. It breaks the cleaning method that requires heating for conventional PCBA water-based cleaning agents. Ideal cleaning effect with short cleaning time and high efficiency.
It has a very good ability to remove various types of no-clean solder paste residues, flux residues, oil stains, fingerprints, metal oxide layers, and particles such as electrostatic particles and dust. With the ultrasonic cleaning process, it can be used for high-cleaning cleaning of camera modules and other high-precision, high-density, assembled with microBGAs, Flip-Chips and other high-tech components
9. ICT test fixture
ICT Test is mainly to detect the open circuit, short circuit and soldering of all parts of the PCBA by contacting the test probe with the test point of the PCB layout.
10.FCT test fixture
FCT (Functional Test) It refers to providing a simulated operating environment (excitation and load) to the test target board (UUT: Unit Under Test), making it work in various design states, so as to obtain the parameters of each state to verify the UUT A method of testing the functionality of a good or bad. Simply put, it is to load the UUT with suitable excitation and measure whether the response of the output terminal meets the requirements.
11. Aging test stand
The aging test stand can test PCBA boards in batches, and simulate the operation of users for a long time to test out the PCBA boards with problems.
12. The cleaning process includes
Wipe the bottom of the solder paste printing machine, clean the solder paste stencil, clean the red glue stencil, clean the fixture carrier, clean the PCB circuit board, etc.
company culture
Jetek Group is a professional manufacturer of PCBs (Included 1-14 layer boards, HDI boards, rigid-flex boards, aluminum boards and so on). Our company was established in 1993 and located in Gaoyao, Zhaoqing. We have a series of fully automatic production equipments and rich PCBs production experience. Flexible order size, fast delivery time, stable quality and competitive price helped us to keep long-term coopertation with our customers.
Technical Information>>
contact us
Jetek Group
Factory 1: No.2, Ma'an Development Zone, 324 National Highway, Gaoyao, Guangdong, China
Factory 2: Building 16, No.16 of Chuangxin Road, Changzhou Street, Rongchang, Chongqing, China
Tel: 008618926528037
Email: mkt01@jetekgroup.com
Overseas Sales Department
Email: info@jetekgroup.com
Tel: +86 0755-23724940
Factory 1: No.2, Ma'an Development Zone, 324 National Highway, Gaoyao, Guangdong, China
Factory 2: Building 16, No.16 of Chuangxin Road, Changzhou Street, Rongchang, Chongqing, China
Tel: 008618926528037
Email: mkt01@jetekgroup.com
Overseas Sales Department
Email: info@jetekgroup.com
Tel: +86 0755-23724940
Products
>>
Copyright © Jetek Group
Address: Building 16, No.16 of Chuangxin Road, Changzhou Street, Rongchang, Chongqing, China
Address: Building 16, No.16 of Chuangxin Road, Changzhou Street, Rongchang, Chongqing, China
本站部分图文来源网络,如有侵权问题请通知我们处理!
网站建设维护